CONSTRUCTION QUALITY CONTROL (QC) MANAGERS
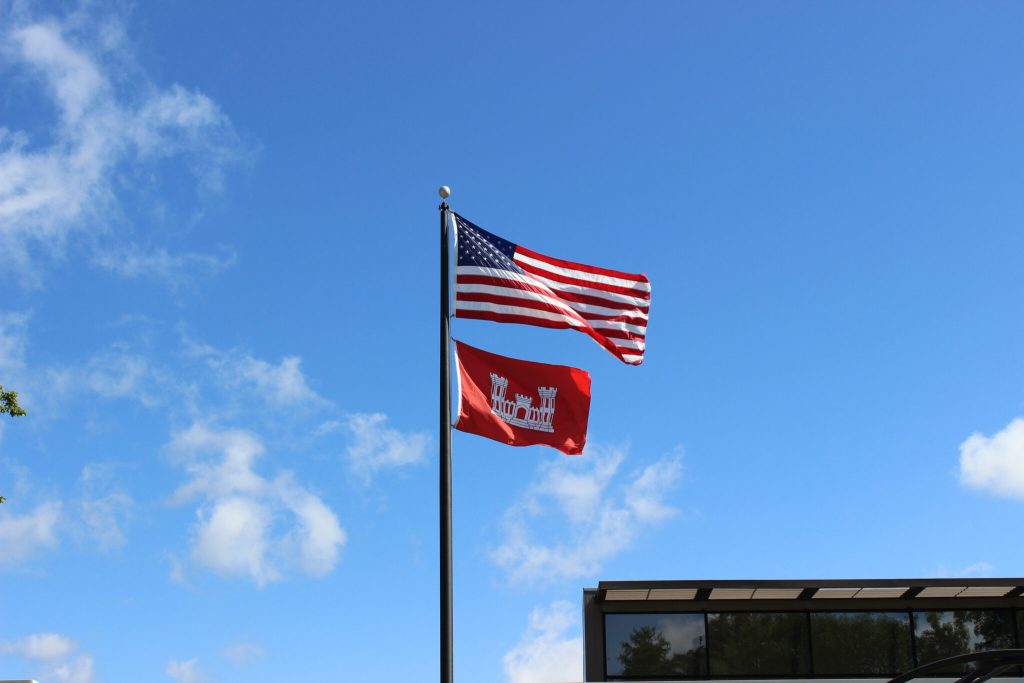
If you are looking to hire a construction quality control manager for your prime contract, you have come to the right place. Our QC Managers are highly skilled in the industry. We work all over the country and abroad. Hire TITAN Consultants for your onsite Construction Quality Control (QC) Manager needs for your prime contract and we will ensure we meet the following requirements on your project:
Utilize, update, and maintain RMS 3.0
Review, approve, reject, and upload submittals in RMS 3.0
Prepare and submit QC daily reports
Conduct daily worksite inspections
Create, utilize, and enforce quality deficiency list
Stop work if quality or safety is operating outside of the contract documents
Conduct 3-phase inspections
Chair and lead weekly progress meetings
Schedule, supervise, and submit testing
Conduct punch-out, pre-final, and final acceptance inspections
Construction Quality Control Manager (CQCM) Job Description and Duties
The CQCM is responsible for managing and performing the daily QC responsibilities of specific projects to ensure the project is constructed in accordance with the established contract documents. The CQCM role includes direct oversight and review of the entire documentation and physical inspection phase of the workflow process and working with other in-house personnel (e.g.: Project Managers, Superintendents, etc.) and external personnel to produce and document a quality product.
Create, update, and maintain the project submittal log and all other project specific quality control reports. Review shop drawings and submittals for conformance with project specifications by direct review, and by leveraging the knowledge and experience of others in the project team when necessary. Chair and document weekly QC meetings with the superintendent, and provide written minutes as described in project specific contract documents. Provide daily QC reports that reinforce activities that are being constructed in conformance with each specific project’s established standard and constructively confronts any non-conformance to produce the desired outcome in a timely manner. Conduct preparatory, initial, and follow-up meetings to establish an understanding of the standards of care desired for each definable feature of work. Verify and document that all materials received for the project are in conformance with the approved submittal, are handled and stored appropriately, and are installed and acceptable for use in the project. Conduct pre-construction meetings with new and existing subcontractors and the superintendent at least two days prior to the start of each new phase of the work to discuss issues that affect quality Coordinate and document the testing and commissioning of building systems Maintain the project “as-built” drawings daily. Assemble and forward project closeout documents that include O&M manuals, as-builts, and warranties Stop work if necessary to resolve matters that affect safety, quality and/or inhibit the logical progress of work.
Required Experience, Education, Skills, and Certifications: Experience working on USACE construction projects with at least 5 years’ experience as a QC manager on USACE construction projects. 15 years’ combined experience as a superintendent, QC manager, project manager, or project engineer on vertical construction and renovation type construction projects Current USACE “Construction Quality Management for Contractors” Certification. Must be able to pass DoD security clearance for base access. Knowledge of a wide range of construction materials, methods, and techniques. Proficiency with RMS 3.0. Proficiency in Microsoft Word, Excel, and Outlook Excellent written and verbal communication. Demonstrate a professional demeanor Valid driver’s license with good motor vehicle record.
We are proud to have worked in the following states:
|
||||
---|---|---|---|---|
We are proud to have worked in the following countries:
Puerto Rico
U.S. Virgin Islands
Guam
Korea
Japan
Afghanistan
Brazil
Frequently Asked Questions (FAQ)
QA stands for “quality assurance”. On USACE and NAVFAC projects, the government has a QA representative onsite to make sure that the QC Manager is doing his/her job. The QA typically reports to the Contracting Officer’s Representative (COR) or Project Engineer on their time at the construction site.
QC stands for “quality control”. The contractor is required under many prime contracts to provide an onsite quality control manager. They are employed by the prime contractor and ensure that all subcontractors and suppliers on the project are working and supplying equipment/materials within the confines of the contract documents.
The USACE/NAVFAC CQM training, also called Construction Quality Management for Contractors (CQM-C #784) course is a requirement for most Quality Control Managers to take and pass in order for the government to consider their approval to work on their construction projects. The course covers all aspects of the QC Manager’s duties and roles in a general sense. If you wish to acquire a more in depth understanding of what it takes to be a QC Manager, please visit www.titansafetycourses.com and view their Quality Control courses.
The certification last for 5 years, starting the day you received your QCM certification. After which, you will have to take the course and pass the exam again to re-certify.
You must schedule and attend any courses hosted by USACE and/or NAVFAC. These courses are only taught by the government. Visit USACE website at https://www.usace.army.mil/Locations.aspx, and find out if there are courses available near you.
Quality control in construction is the systematic process on reviewing and inspecting the construction project daily in an effort to ensure all staked businesses and contractors that are involved with altering the physical property of the project are doing so within the requirements of the contract documents.
Proper quality control ensures that the project is built in accordance to the contract documents. This ensures the government is getting what they are paying for.
The construction quality control manager’s primary duty is to ensure that the project is built per the plans and specifications. On government contracts, the contract documents can be extensive and convoluted at times. The QC Manager is there to ensure the government “gets what they pay for”.
All prime contracts are different. As such, the requirements for the quality control manager can change. But many of the prime contract requirements for quality control managers are: Have and active CQM (#784) certification, have 5 years as a quality control manager or a construction manager with 10 years’ experience, OHSA 30-hr card issued by the Department of Labor, and active first aid / CPR certification.
Most prime contracts do not require a degree. Design-Build deliveries or more complicated prime contracts may require the QCM to have a degree. If this is the case, the requirements for the degree usually require graduate engineer, graduate architect, or a graduate of construction management.